Key Principles Behind Behaviour-based Safety
Behavior-Based Safety refers to the use of applied behaviour analysis models to achieve continuous improvement in safety performance, in-depth research about what works and what doesn't. According to Krause, safety programs fail because they rely too much on antecedents --things that come before behavior -- safety rules, procedures, meetings, and so on.
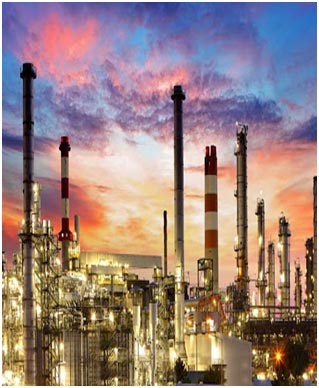
Why BBS?
- Accidents and the related fatalities and injuries are going up.
- To reduce this trend, change in thought process is required.
- More than 90% of the accidents are caused due to unsafe behaviour.
Heinrich’s Theory
- Heinrich’s theory serves as the basis for the behavior-based safety theory.
- This implies that 85 – 90 % of workplace accidents are caused by unsafe behavior.
- On reviewing numerous accident reports, Heinrich concluded that workers were generally responsible for these accidents, but did not investigate the causes.
- Four basic methods are available for preventing accidents: ensuing revision, persuasion, appeal, personal adjustment and discipline.
- Management has the best opportunity and ability to initiate work of prevention there fore it should assume responsibility.
- The supervisor is the key main individual in accident prevention. His application of art supervision for the control of work performance is the greatest influence in successful accident representation and taught as a four step formula -Identify the problem find and verify the reasons for the existence, select the appropriate ready and apply the remedy.
Heinrich’s Pyramid
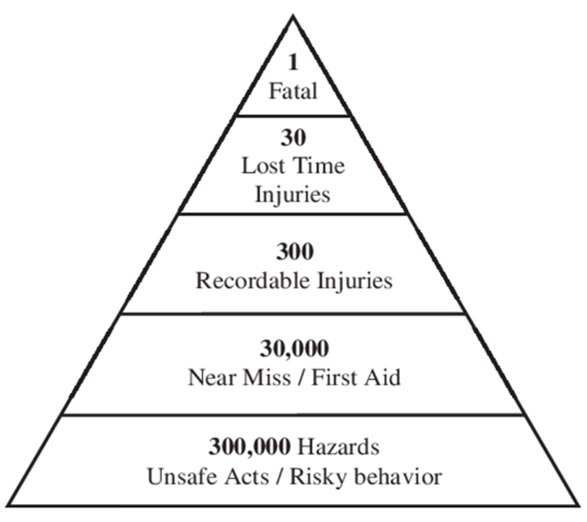
Five stages
- 1. Social environment.
- 2. Faults of a person.
- 3. Unsafe act or condition.
- 4. Accident.
- 5. Injury.
Behaviour Laws
- If the SAFE way is the EASY way, then people will behave SAFELY - behaviour has advantages and becomes habit.
- If the SAFE way is DIFFICULT or uncomfortable, then people will be tempted to behave UNSAFELY - behaviour has disadvantages -unsafe becomes habit.
- If we really understand the consequence of our actions, it will lead to SAFE behavior.
- Behaviours with advantages will be naturally reinforced and become a habit–Behavior has positive consequences.
- Behaviours with disadvantages will be given up–Behavior has negative consequences.
- Behaviours are influenced by expected outcomes–Behavior consequences need to be clear and important.
Principles of Behaviour Safety
- 1. Fully engage employers to the significance of behavioural safety set standards for all employees, at all levels, with participation of all in safe behaviour.
- 2. Careless small behaviours lead to the magnitude of accidents and injuries. Targeting specific behaviour and creating a check list approved by all employees for input creates workplace involvement in safe behaviours.
- 3. Training employees to lead as monitors and active observation and reporting promote employer engagement and compliance.
- 4. Historical review of previous injuries and accident data driven results for decision making.
- 5. Improvement intervention through a systematic observation by employees with regular meetings and brain storming will cultivate continuity of safety based behaviour.
- 6. Provide evolutions to employees or individual practices and safety behaviour.
- 7. Key leadership commitment is important to provide mentioning and examples for employees to commit the idea of working in an environment dedicated to safe behaviour.
ABC Behaviour Model
Antecedents
Antecedents are preexisting sensory or intellectual input that trigger behaviors and influence decision-making
- Can be tangible/concrete or intangible/abstract.
- Only as powerful as the consequences that support them.
Antecedents
- Training .
- Manuals.
- Standard Operating Procedures.
- Feedback.
Behaviour
Behaviour refers to acts or actions by individuals that can be observed by others. In other words, behaviour is what a person does or says.
- Must be observable, measurable.
- Any time, any where, by any body.
Behaviour
- Observable Behaviour : Which can be observed while carrying out work in the factory, control rooms and offices etc.
- Underlying Factor: is related to conditions and work processes that may be “root Causes” of observable behaviour.
Examples
- How well facilities or systems are designed for people’s use Clarity of management’s expectations to follow procedures.
- The effectiveness of the risk assessments in understanding and managing hazards/risks .
Consequence
A consequence is simply what happens to the performer as a result of the behavior.
A consequence can be
Positive or negative: Does the consequence help or hurt from the performer’s point of view?.
Immediate or future: When will the consequence occur?.
Certain or uncertain: What’s the probability that the performer will experience the consequence.
Consequences
- Recognition.
- Rewards.
- Punishment.
- +/- Reinforcement.
Consequence
Positive, Immediate and Certain (PIC) consequences are the most effective consequence for maintaining or increasing performance.
Performance
Performance is composed of a number, or series, of behaviours directed toward some outcome or goal.
BBS Strategies
- Reinforce / create positive consequences for Safe Behaviours.
- Remove negative consequences of desired / Safe behaviours.
- Clarify and Influence perception of potential consequences.
- Create negative consequences for unsafe Behaviour Traditional Safety Management.
- Relies primarily on Strategy #1. Emphasis on antecedents to influence behavior.
- Motivation - avoid negative consequences.
- Occasional negative reinforcement - discipline and loss of rewards. Contemporary Behavior Based Safety Management.
- Relies primarily on Strategies #2 and #3. Emphasis on consequences to influence behaviour. Does not attempt to measure (but does not ignore) attitudes because it’s very complex.
- Motivation. Receive positive consequences .
- Frequent positive reinforcement - frequent recognition and occasional reward.
Dan Petersen’s Three Basic Strategies to Influence Behaviour
- 1. To change attitudes in the belief that our behavior is consistent with our attitudes.
- 2. To build a psychological climate in which people will choose to behave as we wish, since that behaviour helps to satisfy their current needs (We call this motivation).
- 3. To modify behaviour through the systematic use of reinforcement following behaviour to influence future behaviour.
BBS Programme and Cycle
Before starting the BBS program, we tackle any concerns and address any flaws and weakness in current Occupational Health and Safety approaches .
Subsequently we start tracing employers and management to enable them to execute behavioural observations and create self reliance.
BBS Programme
Behavioural observation skills and self reliance by observing behaviour in couples consisting of a Manager and employee. Together they observe other employees and establish + ve dialogues to motivate employees to take the right behavioural decisions. By stimulating such reliance among the work force ,this program enable +ve results on quality and process improvements as well.
BBS Programme
Pinpoint safe behaviours
- Communicate safe behaviours.
- Make behaviour observations.
- Provide Feedback.
Workplace Observations
- To create / Maintain a safe workplace through positive dialogue between observers & the observed BY.
- Recognition of safe behaviour.
- Reciprocal openness and trust (confidence, candor, honesty).
- Cooperative learning .
- Shared identification of hazards and safe(r) work methods
Sample BBS Observation Checklist
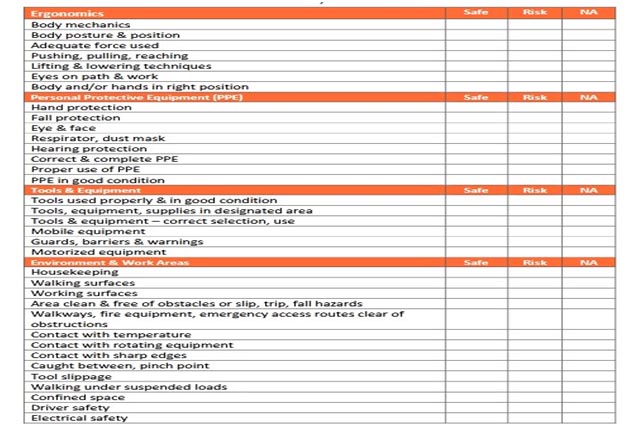
Sample BBS Observation Checklist
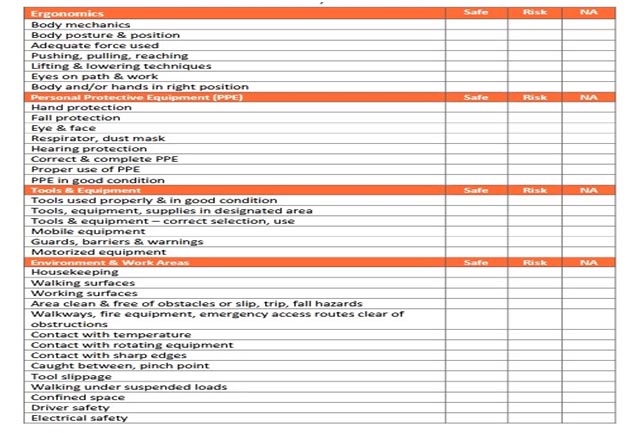
Sample BBS Observation Checklist
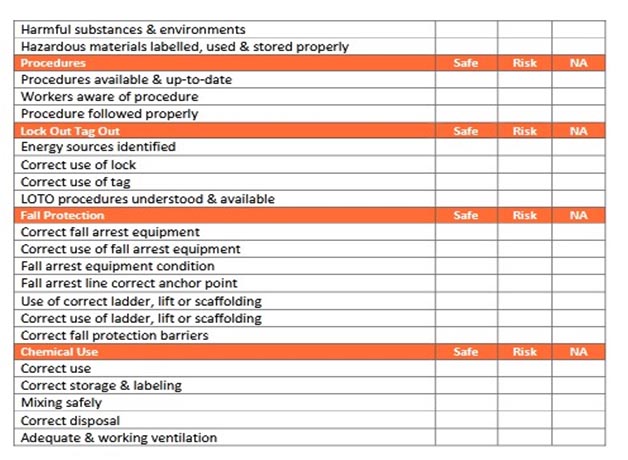
The Safety Improvement Process
- Identify critical problem behaviours. These become action items to work on.
- Identify root causes. The “basic things” that need to be fixed to eliminate the problem.
- Generate potential actions. Think of as many solutions as possible.
- Evaluate possible actions. Choose those that are most productive.
- Develop an action plan. To carry out the chosen solutions.
- Implement the action plan. Carry it the change. Limit variables.
- Conduct follow up. Problem solved? Measure and evaluate.
CASE STUDY
(1) Bhopal Tragedy
(2) L G Gas Accident
Case Study BHOPAL TRAGEDY
- Union Carbide a Joint Venture with Foreign Collaboration stated early in 1969, manufacture Nepthol which is used for Pesticides. MIC an acid is used for the production stored in Tanks.
- In 1976 there was a complaint against Pollution by the Union. In 1982 there was a Phosgene Gas leak and 24 employees hospitalised. In August 1982 a Chemical Engineer met with 30% burns.
- On the Fateful day 2nd December 1984, MIC acid leak. MIC Tank Valves were mis functioning due to corrosion and poor maintenance. Gas started leaking and reported to the Supervisor. In turn he informed to attend the leakage after tea break at 12.40 am. A concrete slab broken was noticed during the time. Due to release of Pressure valves the tank valve bursted and 30 to 40 tonnes of MIC explored to atmosphere in 2 hours time. Two public siren alerted the staff and workers and as well the near by public.
- Due to inhaling of the toxic acid, they had breathing problem and there may be a casuality of more then 20000 where as it was officially reported as 2000. Even after 35 years the people and generations of yesterday and today are suffering the toxic acid and the related diseases.
- The Compensation offered were so low and there is a case pending at the International Court of Law for the Compensation .
Case Study L G Gas – Styrene Gas Tragedy
- There was a Gas Leak on 07 May 2020 at L G Polymer Gas, Visakapatnam. Due to improper maintenance of The Styrene Gas storage tank, there was a vaporisation of the toxic gas between 2.30 to 3.00 am on the fateful day.
- There was no environmental clearance for the unit. The Gas spread over 3 km radius which affected the nearby villages. They had breathing and burning sensation. 100s of people were taken for hospitalisation.
- Expert Team from State and Central Government visited for the spot study. They recorded the gross violation of norms of the organisation. The National Green Tribunal ordered for Interim compensation of Rs. 50 Crores.
- The Court ordered for Closure of the Unit with immediate effect and also to probe the accident and report within 4 weeks time.