Hazard Identification And Risk Assessment Techniques
A hazard analysis used in the first step in a process used assesses their risk. The result of hazard analysis is the identification of different types of hazards. Hazard is a potential condition and exist or not (probability is 1 and 0). It may in single existence or in combination with other hazards (sometimes called events) and conditions become and actual Functional failure or accident (mishap). The way this exactly happens in one particular sequence is called scenario. This scenario has a probability (between 1 and 0) of occurrence. Often a system has many potential failure scenarios.
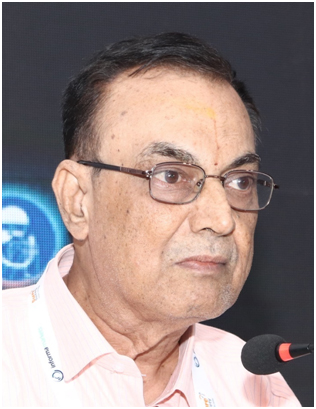
By Venkat Narasimhan, Consultant-International Project Development, UNDP & World Safety Organisation
A hazard analysis used in the first step in a process used assesses their risk. The result of hazard analysis is the identification of different types of hazards. Hazard is a potential condition and exist or not (probability is 1 and 0). It may in single existence or in combination with other hazards (sometimes called events) and conditions become and actual Functional failure or accident (mishap). The way this exactly happens in one particular sequence is called scenario. This scenario has a probability (between 1 and 0) of occurrence. Often a system has many potential failure scenarios. It also is assigned classification, based on the worst case severity. Preliminary risk levels can be provided in the hazard analysis. Validation, more precise prediction (verification) and acceptance of risk is determined in the risk assessment analysis. The Main goal of both to provide the best selection of means controlling or eliminating the risk. The term is used in several engineering specialties including avionics, chemical process safety, safety Engineering, reliability engineering and food safety.
Hazards and risk
A hazard is defined as a" condition, event, that could lead to or to contribute to an unplanned or undesirable event". Seldom does single cause an accident or a functional failure. More often and accident or operational failures as the result of a sequence of causes. Hazard analysis will consider system state, for example operating environment, as well as failures or malfunctions.
While in some cases, safety or reliability can be eliminated; in most cases a certain degree of risk can be accepted. In order two quantity expected costs before the fact, the potential consequences and the probability of occurrence must be considered. Assessment of risk is made by combining of severity of consequence with the likelihood of occurrence in a matrix. Risks that fall into the unacceptable category (example. High severity and high probability) must be mitigated by some means to reduce the level of safety.
What is Hazard identification and risk analysis (HIRA)?
Hazard identification and risk analysis is a collective term that encompasses all activities involved in identifying hazard and evaluating risk at facilities, throughout their life cycle, to make certain that risk to employees, the public are the environmental for consistently controlled within the organisation's risk tolerance.
What do you mean by hazard and risk?
Risk- is there hazard level with(1) the likelihood of the hazard leading to an accident(sometimes called danger) and(2) hazard exposure or duration(sometimes called latency).
How are preliminary risk levels provided in the hazard analysis?
Preliminary risk levels can be provided hazard analysis. The Validation more precise prediction (verification) and acceptance of risk is determined in the risk assessment (analysis).The main goal of both is to provide the best selection of means of controlling for eliminating the risk.
Inductive and deductive:
The Main difference between inductive and deductive reasoning is that reasoning aims at developing a Theory while deductive reasoning aims at testing an existing theory. Inductive reasoning moves from specific observations to broad generalizations, and deductive reasoning other way around.
Is there difference between inductive and deductive reasoning?
While much of our reasoning is done consciously, we also use reasoning skills constantly without realizing it. There are two main types of reasoning inductive and deductive. In this article, we will define types of reasoning and the differences between them.
Which is the best definition of the inductive method?
Many sources may define the inductive method as one in which general principles or derived from specific observations. In this method broad generalizations are made from specific observations, so that it can be said that goes from the specific to the general.
What is the difference between inductive and top-down logic?
Deductive reasoning (top-down logic) contrasts with inductive reasoning (bottom up logic),and generally starts with one or more general statements or premises to reach logical conclusion. If the premises are true conclusion must be valid.
How is the inductive study followed up with deductive research?
The Inductive study followed up with deductive research to confirm or invalidate big conclusion. In the examples above, the conclusion (theory) of the inductive study is also used as a starting point for the productive study.
How is the inductive study followed up with deductive research?
The Inductive study followed up with deductive research to confirm or invalidate big conclusion. In the examples above, the conclusion (theory) of the inductive study is also used as a starting point for the productive study.
Inductive reasoning:
Reasoning in artificial intelligence as two important forms, inductive reasoning and deductive reasoning. Both reasoning forms have premises and conclusions, but both reasoning are contradictory to each other. Following is a for comparison between Inductive and deductive reasoning:
- Enforcing Guidelines Related to Employee Safety and Industrial Hygiene: Key Challenges and Responsibilities (panel discussion).
- Deductive reasoning uses available facts, information, or knowledge to deduce valid conclusion, where inductive reasoning is involves making a generalization from specific facts and observations.
- Deductive reasoning uses a top down approach, where as inductive reasoning uses your bottom- up approach.
- Deductive reasoning, moves from generalized statement a valid conclusion, where else inductive reasoning most from specific observation to generalization.
- In deductive reasoning the conclusions are certain, whereas, inductive reasoning, the conclusions probabilistic.
- deductive argument can be valid or invalid, which means if premises or true, the conclusion must be true where as inductive argument can be strong or weak,which means conclusion maybe Falls even if premises are true.
Comparison chart:
Basis for comparison:
Deductive reasoning:
Definition
Deductive reasoning the form of valid reasoning, to deduce new information for conclusion from non related facts and information.
Inductive reasoning arrives at a conclusion by the process of generalization using specific facts or data.
Approach
- Deductive reasoning follows a top-down approach.
- Inductive reasoning follows bottom down approach.
Starts from
- Deductive reasoning starts from premises.
- Inductive reasoning starts from the conclusion.
Validity
- In deductive reasoning conclusions must be true if the premises are true.
- In inductive reasoning the truth of premises does not guarantee the truth of conclusions.
Usage
- Use of deductive reasoning is difficult, as we need facts which must be true.
- Use of inductive reasoning is fast and easy, as we need evidence instead of true facts. We often use it in our day to day life.
Process
- Theory- hypothesis- patterns- confirmation.
- Observations- hypothesis- theory.
Argument
- Deductive reasoning, arguments maybe valid or invalid.
- Inductive reasoning or maybe weak or strong.
Structure
- Deductive reasoning reaches from general facts specific facts.
- Inductive reasoning reaches from specific facts to general facts.
- Inductive method detective method: Are the two approaches opposed to Investigation.
Each method has its advantages and its use will depend upon on the situation to be investigated. Field study you want to study the Approach you want to have.
Deductive reasoning works by working most general to the most specific. You can begin thinking of your theory on some topic of interest. It then boils Down to some specific hypothesis that you want to test. On the other hand the inductive method works in the opposite way: It starts from the most Specific to the generalization and broader theories. In inductive reasoning.
We begin with specific observations and measures to arrive at some general conclusions. These two methods are very different and offer different elements when Carrying out an investigation. By its nature, inductive reasoning allows More flexible and lends, to the exploration mainly at the beginning.
That deductive method is closer by nature and is more oriented to test or confirm hypothesis.
All too some particular study seems purely deductive, as an experiment designed to test the hypothetical effects of some treatment or outcome, Most social research requires both deductive reasoning and inductive reasoning.
Concept of inductive method and deductive method :-
Inductive reasoning is the reasoning in which premises are viewed as a way of providing strong evidence for the truthfulness of a conclusion. While the conclusion of inductive argument is certain, the truth of the Conclusion in an inductive argument is likely, based on the evidence provided. Many sources may define inductive method as one in general principles or derived from specific observations. In this method, broad generalizations are made from specific observations so it can be that it goes from the specific to the general. Many Observations are made pattern is perceived, a generalization is made an explanation or a theory is inferred. This method is also used in the scientific method. Scientists used to form hypothesis and theories. Deductive reasoning allows them to apply theories or assumptions to specific situations. An example of deductive reasoning may be as Follows:
All known-biological forms depend on liquid water to exist. Therefore if we discover new biological life form it will depend on liquid water to exist. This argument could be made every time a biological form of life is found and would be correct. However, it would be possible on the future find Biological life form that does not require liquid water.
Failure mode effect analysis
Failure mode and effects analysis (FMEA: Often written with failure modes in plural) is the process reviewing as many components, assemblies, and subsystems, as possible identify potential failure modes in a system and their causes and effects.
What is the difference between a FMEA and effects analysis?
Jump to navigation, Jump to search, Failure mode and effect analysis (FMEA: Often written with failure modes in plural) is the process of reviewing as many components, assemblies and subsystem as possible to identify potential failure modes in a system and their causes and effects.
What is the difference between and FMEA and failure mode?
A FMEA example an approach to identify all possible failures in a design, assembly process, or in the product. Failure mode is describing an error in the product that can be potential or actually exist that will affect the customer. Effects analysis is studying the effect of these errors.
Can a failure have more than one effect?
If a failure mode as more than one effect, right on the FMEA table only the highest Severity rating for that failure mode. For each failure mode, determine all the potential root causes. Use tools classified as cause analysis tools, as well as the best knowledge and experience of the team.
Which is the best management tool to analyze failure modes?
Failure mode and effects analysis is one of the best management tools to analyze the potential failure modes within a system under conditions of uncertainties, as stated above. Its principle is quite basic, and has been practiced since the olden days as the trial and error method.
Failure mode effect analysis:
Failure mode and effects analysis (FMEA: Often written with failure modes in plural) is the process reviewing as many components, assemblies, and subsystems, as possible identify potential failure modes in a system and their causes and effects.
What is the difference between a FMEA and effects analysis?
Jump to navigation, Jump to search, Failure mode and effect analysis (FMEA: Often written with failure modes in plural) is the process of reviewing as many components, assemblies and subsystem as possible to identify potential failure modes in a system and their causes and effects.
What is the difference between and FMEA and failure mode?
A FMEA example an approach to identify all possible failures in a design, assembly process, or in the product. Failure mode is describing an error in the product that can be potential or actually exist that will affect the customer. Effects analysis is studying the effect of these errors.
Can a failure have more than one effect?
If a failure mode as more than one effect, right on the FMEA table only the highest Severity rating for that failure mode. For each failure mode, determine all the potential root causes. Use tools classified as cause analysis tools, as well as the best knowledge and experience of the team
Which is the best management tool to analyze failure modes?
Failure mode and effects analysis is one of the best management tools to analyze the potential failure modes within a system under conditions of uncertainties, as stated above. Its principle is quite basic, and has been practiced since the olden days as the trial and error method.
Failure mode effect analysis (Wikipedia)
Failure mode effect analysis is often written as failure modes in plural is the process as many component, assemblies, and subsystems as possible to identify potential failure modes in a system under causes and effects. For each component the failure modes and the resulting effects on the rest of the system are recorded in a FMEA worksheet. There are numerous variations of such worksheets. An FMEA can be a qualitative analysis but maybe put on a quantitative basis when mathematical failure rate models for compound with statistical failure mode ratio database. It was one of the highly structure, systematic techniques for failure analysis. It was developed by reliability engineers in the late 1950s to study problems that might arise from Mall functions of military system. And FMEA often first step of system reliability study.
A few different types of FMEA analyses exist, such as
- Functional
- Design
- Process
Sometimes FMEA is extended to FMECA (Failure mode, effects and Criticality analysis) to indicate that critical analysis is performed too.
FMEA is an inductive reasoning (forward logic) single point of failure analysis is a core task in reliability engineering, safety Engineering. , And quality engineering.
A successful FMEA activity helps potential failure modes based on experience switch similar products and processes- or based on uncommon physics of failure logic. It is widely used in the development and manufacturing industries in various phases of the product life cycle. Effects analysis refers to studying the consequences of these failures on different system levels.
Functional analyses are needed as an input to determine correct failure modes at all system levels, both for functional FMEA or piece part (hardware)FMEA. An FMEA is used to structure mitigation for Risk reduction base on either failure mode affect severity or based on either the probability of failure or both. The FMEA is in principle f full inductive (forward logic) analysis; however the failure probability can only be estimated or reduced by understanding the failure mechanism. Hence FMEA may include information on cause of failure(detective analysis) to reduce the possibility of occurrence eliminating identified root causes.
Introduction
The FME(C) A t-shirt design tool to systematically analyze postulated component failures and identify the resultant effects on system operations. The Analysis Sometimes characterized as consisting of two Sub-analyses, the first being the failure modes and effects analysis (FMEA), and the second, the criticality analysis (CA). Successful development Of an FMEA requires that the analyst include all significant failure modes for each contributing element or part in the system. The FMEAS can be performed at the system. Subsystem, assembly, sub-assembly or part level. The usefulness of the FMECA should be a living document during the development of a hardware design. It should b scheduled and completed concurrently with the design tool and in the decision making dependent on the effectiveness and timeliness with which design problems are identified. Timeliness is probably the most Subsystem;
Remark
For complete scenario modeling type of Reliability analysis may be considered, for example fault tree analysis, deductive (backward logic) failure analysis that handles multiple failures within the item and/ or external to the item including maintenance and Logistics. It starts at Higher functional/ system level. Fault tree analysis basic failure mode FMEA records or an effect summary as one of its inputs (the basic events) interface hazard analysis, human error analysis and others may be added completion in scenario modeling.
The analysis should always be started by listing the function that the design needs to fulfill. Functions or the starting point of a well done FMEA, and using functions as baseline provide the best yield of an FMEA. After, all only one design is possible solution to perform functions that need to be fulfilled. This way an FMEA can be done on concept designs as well as retail designs, on hardware as well as software, no matter how complex the design. When performing and FMECA, interfacing hardware (or software) is first considered to be operating within specification. After that it can be extended by consequently using one of the 5 failure modes of one function of interfacing hardware as a cause for failure of father design element under review. This gives the opportunity to make the design robust for function failure elsewhere in the system.
In addition each part of failure postulated is considered to be only failure in the system (that is, it is a single failure analysis). In addition to the FMEAS turn on systems to evaluate the impact lower level file use have on system operation, several other FMEAS are done. Special attention field interfaces between systems and in fact at all functional interfaces. The purpose of this FMEAs east towards assure that Irreversible physical and/ or functional damage is not propagated across the interface as a result of failure in one of the interfacing units. These analyses or done to the Piece part level of the circuits that directly interface with other units. The FMEA can be accomplished without your CA, but a CA requires that FMEA has previously identified and system level critical failures. When both steps and done total process is called FMECA.
Ground rules
Ground rules of each FMEA include a set of project selected procedures, the assumptions on which analysis is based: The hardware that has been included and excluded from the analysis and there rationale for the exclusions. The ground rules are described that indenture level of the analysis (that is the level in the in the hierarchy of the path to the subsystem, subsystem to the system etc.). The basic hardware and the criteria of the system mission success. Every effort should be made to define all ground rules before the FMEA begins; ground rules may be expanded clarified as the analysis proceeds. Typical set of ground rules follows.
- Only one failure mode exits at a time.
- All inputs (including software commands) to the item being analyzed or present and at nominal values
- All consumables or present in sufficient quantities.
- National power is available
Benefits
Benefits derived from a properly implemented FMECA effort are as follows.
- It Provides document third method for selecting the design high probability of successful operation and safety.
- Documented uniform method of assessing potential file your mechanisms, failure modes and their impact on system operation, resulting in a list of failure modes ranked according to the seriousness of their system impact likelihood of occurrence.
- Identification of single failure points, system interface problem which may be critical to the success of the mission and safety. They also provide a method of verifying that switching redundant elements not jeopardized postulated by single failures.
- And effective method for evaluating effect of proposed changes to the design and or operational procedures on Mission success and safety.
- Basis for in-flight troubleshooting procedures and locating performance monitoring and fault detection devices.
- Criteria for early planning test. From the above list, identifications of SFPS input to the troubleshooting procedures and locating of performance monitor / fault detection devices or probably the most important benefits of FMECA. In audition the FMECA procedures or straight forward and allow orderly evaluation of the design.
Fault tree analysis
Fault tree FTA top down detective failure analysis in which an undesired system state of a system is analyzed using Boolean logic. This analysis mainly used in the fields of Safety Engineering and reliability engineering understand house systems can fail to identify the best. To reduce risk or to determine even rates of safety accident or a particular system (level) functional failure. FTA is used in aerospace, chemical process industries pharmaceutical, nuclear power, and other high hazard industries.
But is also used as derived as risk factor. Identification relating to social service system failure. FTA is also used in software engineering for debugging purposes and is closely related to cause elimination technique used to deduct bugs.
In aerospace industry system failure condition is used for the undesirable state. Classified by severely of their effects. The most other severe conditions required most expensive fault tree analysis’ System failure conditions and their classification of functional hazard analysis.
- Usage
- History
- Methodology
- Graphic symbols
- Event symbols
- Gate symbols
- Basic mathematical Foundation
- Analysis
Subsystem
Usage.
- To understand logic leading to the top event/ undesired event
- Allow compliance with input system safety / reliability requirements.
- Prioritize the contribution leading to top event- critical equipment's/ parts/ events for different reasons.
- Monitor and control the safety performance of the complex system(e.g) is a particular aircraft to fly when fuel valve malfunctions. For how long it is allowed to fly with the valve malfunction.
- Minimize and optimize reasons.
- To design a tool that helps to create (output/ lower level) requirements.
- Function as a Diagnostic tool to identify and correct causes of the event.
History
For tree analysis was originally developed in 1962 at Bell Laboratories under a air Force the use of fault tree. The Use of fault tree analysis since gained wider support and is often used as a failure tool by reliability engineers.
Early in the Apollo project the probability of successfully sending astronauts to the moon and return them safely to earth. In 1983 challenger probabilistic risk assessment and FTP in systems and risk and reliability analysis was realistic. And now if FTA is considered one of the important system reliability and safety techniques.
The process industry such as 1984 Bhopal disaster and 1988 alpha Piper explosion.
Methodology
Any difficulty complex system is subject to a failure as a result of one or more subsystem failing. The likelihood of failure however can be reduced through improved design system. Fall tree analysis the relation between facts, subsystems, and redundant safety system design elements by circulating logic diagram.
The Undesired event outcome is top event of the logic. For instance desired outcome of a metal Stamping. Phase operation is being stamped working backwards top event, we might determine there are two ways could happen. During operation or doing maintenance operation. The condition logical is R. Consider the branch of occurring during normal operation perhaps we determine two ways this could happen. The press cycle and harm the operator or press the cycles and harm another person. This is logical R. We can design the operator press two buttons to cycle the machine. This is a safety feature by logical And. The bottom may have intrinsic failure rate. When Fault lines are labeled with actual numbers for failure probabilities. Computer program can calculate failures from fault tree lines. When Specific event is found to have more than one effect, that is has effect on subsystem.
Graphic symbols
Basic symbols used in FTA grouped.
Events, gates and transfer symbols.
Symbols or used as primary events.
Basement
Failure or error in a system component or element (switch in stuck up position)
External fault: Normally expected to occur (not itself to a fault)
Underdeveloped events
An event about which insufficient information is available of which no consequences.
Gate symbols
Gate symbols derive the relationship between input and output events. The gates are worked as follows :-
- OR gate-The output the occurs if any input occurs.
- And Gate- the output occurs only if all inputs occur (inputs are independent).
- Exclusive-OR gate- the output occurs if exactly or in input occurs.
- Priority AND gate- the output occurs if the input occurs under on conditions specified by a conditioning event.
Transfer Symbols :-
Transfer Transfer out
Basic mathematical function:
Events in a fault tree or associated with statistical probability.
Unlike conventional logic Gate diagrams which inputs and outputs holds the binary valves of True or False. The greats in a format or tree probabilities relates to set operation.
An AND gate represents combination of independent events. That is the probability any input event to an AND gate is an affected by an input to the same Gate insert operation terms. This is equivalent to the interest section of the input event and the probability of the AND gate output is given by.
p (A and B)= p(A*B)=p(A) p(B)
An OR gate, on the other hand corresponds to set Union.
p(A or B) An exclusive OR gate with two inputs represents that one or the other input not both occurs. p (A* or B)p(A)+p(B)-2p(A*B)
Analysis :-
FTA is normally used for more undesired events
1. Define the undesired even to study.
An engineer with wide knowledge of the design of the system or a system analyst with an engineering background who can help the design events. Undesired events are making FTA.
2. Obtain the understanding of the system computer software is used to study the probabilities that may lead to costly the system analysis.
3. Construct the fault tree
After selecting the undesired event and having analyzed the system that we know the coughing effects. Fault tree is based on AND and GATES which define the major characteristic of the fault tree.
4. The fault tree:
After the fault tree has been assembled for a specific undesired event it is evaluated and analyzed in order to study the risk management. Quantitative and qualitative methods can be applied. The final step is to control the hazards identified.
5 control the hazards identified;
This step differ from others system after identifying, what the main point will always be after identifying all possible methods pursue to decrease the probability of the occurrence.
Maximum Credible Analysis:
Maximum credible accident analysis is carried out to at the hazard distance for the worst case scenario. Maximum credible accident analysis is a probable accident with maximum damage distance. In practice, the selection of accident scenarios for MCAA is carried out on the basis of engineering judgment and past accident analysis. MCC does not include qualification of the probability of occurrence of an accident.
What is the maximum credible event for explosives?
Any important explosive safety functions such as odd analysis, explosive hazard classification and facility citing or base on the anticipated maximum credible event. This paper focuses on the maximum credible event for hazard division explosive articles.
What is the maximum credible event even in the DOD?
Maximum credible event DOD 6055.09-STD defines the term maximum credible event as it relates to explosives.
What is the maximum credible even for a Hazard division?
DOD 6055.09 STD defines maximum credible event as it relates to explosives.
Examples of each audit:
Audit procedures normally design to confirm financial assertion of transactions or events in the financial statements. For example the auditor main test the occurrence of sales revenues that records in the income statement for this test East confirm whether those transactions have really occurred or not.
What are the different types of audit used?
There are various types of audits. However in most all of them auditors use different processes, tests, techniques, or methods. As stated, the main goal of these techniques and methods is together audit evidence to base their opinion on and use in the audit report.
Which is the best example of external audit?
The external audit is a type of audit service that audit form provides Assurance service, consultant service, taxi service, legal service, financial advisory and risk management advisory. The best example of external auditing is the services by providing this big 4 audit firm including KPMG, PWC , EY, and Deloitte.
Who are the parties that need to be audited?
Sometimes, other parties, including shareholders, financial institution, creditors, etc, may also require an audit of the financial institution statements of the company before trading with it. Various types of audits. However, in almost all of them, auditors use different processes, test, techniques, or method.
What should we include in audit report?
Objectives should always be return in a way that will allow audit us to provide informative conclusions to the audit reports audience. In particular auditor should avoid objectives that only killed yes / no answers.
Chemical safety standards:
We are committed continual innovation and development of safer working conditions and working practices and safe safer handling of chemicals in the workplace. Our management safety process or therefore based on internationally chemical safety standards, developed by the leading global industries regulatory bodies.
Will you pass your next chemical safety audit?
Greater regulatory pressures and ever changing of picture of industry standards, means that that it is very important ever to work effectively to identify all areas of your working operation whereas safety moments can be achieved. To this end, chemical safety audits from Chem. alert software provide invaluable Insight into you are established chemical safety standard and procedures identify and help all areas in which issues of non compliance have arisen. Our team of experienced Chem. Alert chemical auditors will work with you to establish tradition of safety within your workplace.
The establishment effective workplace procedures are essential to ensure yourworkforce safety.
Benefits of chemical safety auditing include
- An extensive report how to achieve regulatory compliance where necessary.
- Intimate picture of chemical management procedures.
- A further understanding of the effects of the internationally established GHS on your regulatory obligations.
- Advice recording you are Dangerous Goods Segregation, separator, placarding requirements.
- Advise pertaining safety management hazardous chemicals within the workplace Chemical safety audit process and outcomes.
- Investigation and assessment chemical safety management processes, using internationally standard including GHS regulatory practices.
- Invaluable on site guidance and advice regarding critical chemical safety issues in your operations which require immediate attention.
- the compilation of comprehensive chemical safety audit report providing recommendations for the achievement of regulatory compliance, and establishment the safe working procedures, and .
- show Singh collating and delivering of SDS and MSDS for all specific chemicals through the Chem. Alert online system
Chemical safety best practices
- Over exposure two chemical substances may cause acute or chronic health damages. Follow this general tips to protect yourself from chemical hazards.
- ensure chemical containers clearly labeled.
- inspect containers for leaks or damage.
- keep containers tightly closed when not in use.
- as much as possible your exposure to a chemical substance.
- read the label and follow instruction carefully.
- ensure proper ventilation.
- cautious of health symptoms.
- wear appropriate personal protective equipment.
- proper training of chemical handling.
- aware of first aid procedures.
- do not return contaminated or unused material to the original container.
- use proper tool to open chemical containers to prevent spillage.
- pouring chemical substance handle with care to avoid splashing and spurting.
- keep the working area clean.
OSHA hazardous chemical exposure checklist
Exposure checklist is self inspection checklist can be used as a safety precaution before handling chemical substances. And sure that trained and fully equipped personal will be performing the task. Check chemical containers for leakage, damage or dents and if the work area has a proper ventilation system installed.
PPE checklist:
Most chemicals can enter the body skin absorption, inhalation, and ingestion. Mishandling Of chemical substance over lead employees to serious injuries or PL. Wearing appropriate personal protective equipment like safety gloves, suits, goggles and face masks can help to eliminate this hazards.
Accident report form checklist
Accidents and injuries or common in workplaces when chemical safety procedures were not followed. Compile accident records for your organization track the improvement of safety. Documents sick the weekend data of the injured person, injury details and witness statements and factors that contributed to the incident also record hospitalization and witness document for more accurate information.
Measures and Controlling Processes
Project management time of action off monitoring controlling process force to particular process that are implemented by the project team and or the project team leader soul and explicit purposes are of taking a careful measurement of unto complete thorough monitoring of the team project execution to date. The purpose of the project teams implementation off monitoring and controlling processes include retrospective view in hopes of potentially implementing corrective action in the event of any action of this type is deemed necessary. This can be the case when any particular page of the project has taken wrong Turn or possibly fallen begin schedule in regard to the execution of the project. The act of monitoring and controlling project process is essential to maintaining an efficient and effective workflow throughout the project. At the onset of the project team leader main as a nor one or more project team members to be responsible for this activity.